Step 2: Conjugate Heat Transfer
Complete input file for this step: 02_core.i
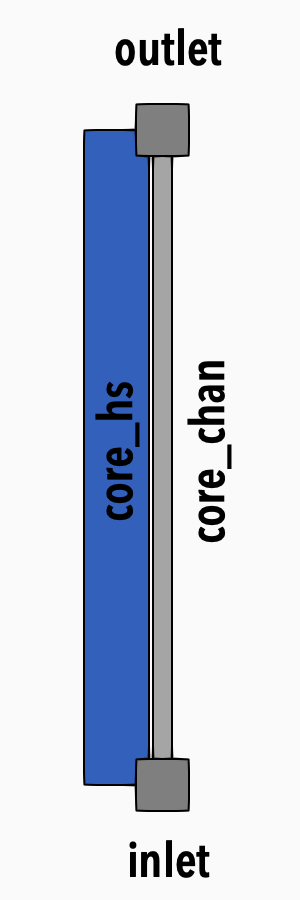
Figure 1: Model diagram
In this step, we will add a heating block to our flow channel, set up heat source, and connect the solid block to the flow channel via conjugate heat transfer.
Parameters of the Heated Channel
We include the core parameters as named parameters to the top of the input file as follows:
core_length = 1. # m
core_n_elems = 10
core_dia = ${units 2. cm -> m}
core_pitch = ${units 8.7 cm -> m}
For total power used for heating the block, we prescribe a parameter called tot_power
.
tot_power = 100 # W
Heat Structure Materials
To set up a heat conduction, we will need to define a solid material used in the block with heat conduction. To do that, we put the following block into a top-level [HeatStructureMaterials]
block:
[steel]
type = SolidMaterialProperties
rho = 8050
k = 45
cp = 466
[]
where rho
, k
, and cp
are density, thermal conductivity, and specific heat, respectively. The name steel
is arbitrary and is used to refer to this material from other parts of the input file.
Heat Structure
A heat structure is a 2D or 3D component that is used for modeling heat conduction. In our setup, the heating block is a rod, so we use HeatStructureCylindrical
for the model. The component takes the position
parameter, which is the location in 3D space. The orientation
parameter is the axial directional vector, length
is the axial length, and n_elems
is the number of elements in the axial direction.
The number of axial elements must match the number of elements in the flow channel.
In radial direction we define one block called block
and assign our previously defined steel
material to it. The number of radial element in this block will be 3
.
[core_hs]
type = HeatStructureCylindrical
position = '0 0 0'
orientation = '0 0 1'
length = ${core_length}
n_elems = ${core_n_elems}
names = 'block'
widths = '${fparse core_dia / 2.}'
materials = 'steel'
n_part_elems = 3
[]
Heat Source
Our heating will be given by the specified total power parameter. For this, we need to include TotalPower
component and link it with another component – HeatSourceFromTotalPower
.
[total_power]
type = TotalPower
power = ${tot_power}
[]
[core_heating]
type = HeatSourceFromTotalPower
hs = core_hs
regions = block
power = total_power
[]
HeatSourceFromTotalPower
needs to know which heat structure and which part it acts on, which is done via the hs
and regions
parameters. The link to the TotalPower
component is created via power
parameter which takes the name of the TotalPower
component.
Heat Transfer
To exchange heat between a flow channel and heat structure, we use the HeatTransferFromHeatStructure1Phase
component. We need to specify the flow_channel
parameter which takes the name of the connected flow channel, hs
parameter which is the name of the heat structure component, hs_side
parameter which is the side of the heat structure and can be either inner
or outer
.
Lastly, we need to specify P_hf
, which is the heated perimeter, and because we are using simple
closure we need to supply Hw
, which is a convective wall heat transfer coefficient.
[core_ht]
type = HeatTransferFromHeatStructure1Phase
flow_channel = core_chan
hs = core_hs
hs_side = outer
P_hf = '${fparse pi * core_dia}'
Hw = 1.36
[]
This concludes the step of coupling a flow channel with a heat structure.