Lead-Rubber Isolator
Lead-rubber (LR) seismic isolators are composed of alternating layers of natural rubber and steel shims with steel flange plates at top and bottom, and a central cylindrical lead core. Continuum modeling of LR bearings is computationally expensive and impractical for applications involving large structures with tens to hundreds of isolators. Hence, the two-node model developed by Kumar et al. (2015) is adopted here. The isolator model has six degrees of freedom (3 translations and 3 rotations) at each node and is capable of simulating nonlinear behavior in both axial and shear directions. The physical model of the two-node isolator element is shown in Figure 1 below. For a detailed description on the implementation of numerical model, refer to (Kumar et al., 2015).
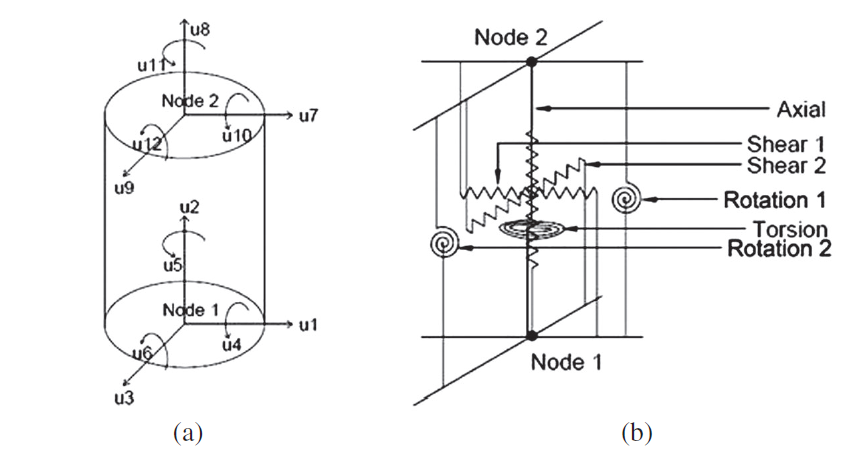
Figure 1: Discrete, two-noded model of an LR bearing: (a) degrees of freedom, and (b) discrete spring representation (Kumar et al., 2014).
This model captures the following physical behaviors:
Axial
Buckling in compression
Buckling load variation with shear deformation
Cavitation and post-cavitation behavior in tension
Shear
Viscoelastic behavior of rubber
Hysteretic behavior of the lead core
Strength degradation due to the heating of the lead core
Coupling in axial and shear
Shear stiffness variation with axial load
Axial stiffness variation with shear deformation
Axial (local X direction)
Compression
The composite action of the rubber and the steel shims result in high axial stiffness of a bearing. The expression for the critical buckling load in compression is derived from the two-spring model proposed by Koh and Kelly (1987) as shown in Eq. (1).
(1)
where,
Eq. (1) provides the critical buckling load at zero shear displacement. Experimental investigations have shown that the critical buckling load is a function of the shear deformation. Warn and Whittaker (2006) proposed a simplified expression for the critical buckling load as a function of the overlap bonded rubber area. The critical buckling load is updated at every analysis step based on the current shear deformation in the bearing.
(2)
where,
is the rotational modulus
is the height of isolator excluding the end plates
is the total rubber thickness
is the shear modulus of the rubber
is the initial bonded rubber area
is the current value of the critical buckling load
is the critical buckling load at zero shear displacement
is the current overlap area of bonded rubber
Once the bearing buckles, the axial stiffness is reduced to zero. However, to avoid numerical problems, a very small value of axial stiffness is assigned to the post-buckling region.
Tension
Beyond a certain tensile stress, rubber undergoes cavitation, which is an expansion of existing voids or defects in the material. Cavitation results in an inelastic deformation due to the onset of permanent damage. The LR isolator exhibits linear elastic behavior, till the point of cavitation (,), where, and are the deformation and force, respectively, at the onset of cavitation. Due to the breakage of rubber-filler bonds, the post-cavitation stiffness is reduced. Constantinou et al. (2007) suggested an expression for post-cavitation stiffness as:
(3)
Integrating the Eq. (3), the expression for the post-cavitation tensile force is obtained as:
(4)
where,
is the initial cavitation force
is a cavitation parameter
is the initial cavitation deformation
is the tensile deformation
is Young's modulus of the rubber
When the bearing is loaded beyond the point of cavitation and unloaded, it does not unload with the initial elastic stiffness. The unloading stiffness is smaller than the elastic stiffness because of formation of cavities in the rubber. The cavitation strength is a function of a damage parameter which varies from zero to one. At maximum damage, the tensile strength of rubber layers is not completely zero. Therefore an upper bound of 0.75 value is assumed for the damage parameter.
(5)
where,
is the damage constant
is the current value of the damage parameter
is the upper bound on the damage parameter
For (namely, at the cavitation point), is equal to 0 implying no damage. As the tensile deformation increases, the damage parameter converges to . The reduced cavitation strength as a function of damage parameter is calculated as
(6)
Figure 2 shows the assumed response of a LR isolator to cyclic axial loading (both compression and tension).
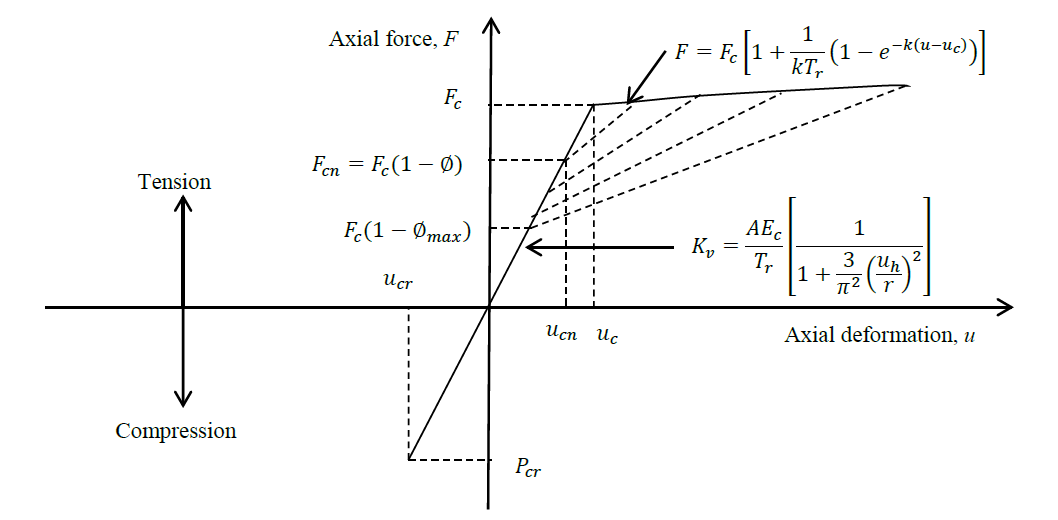
Figure 2: Axial response of an elastomeric isolator (Kumar et al., 2014).
where,
is the axial stiffness of the isolator
is the current shear deformation
is the radius of gyration of the isolator
Shear behavior (local Y and Z directions)
The smoothed hysteric model proposed by Park et al. (1986) and extended by Nagarajaiah et al. (1989) is used to model the behavior of a lead-rubber bearing in shear. The shear resistance of the LR bearing is a combination of the viscoelastic behavior of the rubber layers and the hysteretic behavior of the lead core, as shown in Figure 3. The behavior of rubber is characterized by elastic stiffness, viscous damping terms and the nonlinear hysteretic contribution of the lead core is modeled using a Bouc-Wen formulation.
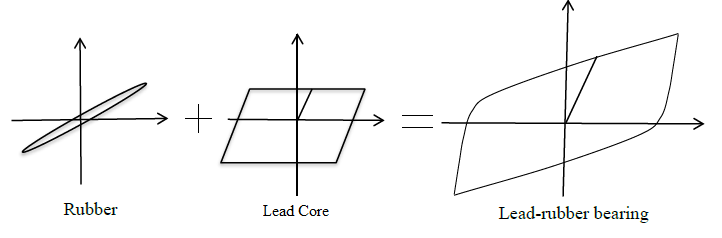
Figure 3: Shear behavior of the LR isolator (Kumar et al., 2015).
(7)
where,
subscripts and correspond to shear 1 (local Y) and shear 2 (local Z) directions respectively, as shown in Figure 1
is the viscous damping co-efficient of the rubber</br> is the shear stiffness of the rubber material </br> is the dynamic yield strength of the lead core </br> is the cross sectional area of the lead core
The Bouc-Wen formulation introduces two hysteresis evolution parameters, and , which are functions of the shear displacements and , in the local Y and Z directions respectively.
(8)
where,
(9)
Eq. (8) is iteratively solved using the Newton-Raphson method to calculate the values of and at every analysis step in MASTODON.
Lead core heating
When the LR isolator is subjected to cyclic loads in shear, the temperature of the lead core increases. The effective yield stress of the lead core used in Eq. (7) varies with the temperature of the lead core, which is a function of time. Therefore, at every time step, the temperature of lead core is calculated and the dynamic yield strength of the lead is adjusted. The relationship between the dynamic yield strength of the lead core and the instantaneous temperature was proposed by Kalpakidis and Constantinou (2009a) as
(10)
where,
is the dynamic strength of lead core at the current temperature
is the dynamic yield strength of lead core at a reference temperature
is the instantaneous temperature of the lead core
Coupled shear and axial response
When the axial load on the bearing is close to the critical buckling load, the shear stiffness of the rubber is reduced substantially. This reduction in shear stiffness as a function of axial load is approximated using the equation from Kelly (1993).
(11)
where,
P is the current axial load on the isolator
The axial stiffness of the LR isolator is also a function of the overlap bonded rubber area, which is a function of the shear deformation. A simplified expression formulated by Koh and Kelly (1987) and Warn et al. (2007) is adopted here (12)
where,
is the current shear deformation
Limitations
Currently, this formulation is limited to simulations that result in small rigid-body rotations in the isolator because the isolator deformations are transformed from the global to the local coordinate system using a transformation matrix that is calculated from the initial position of the isolator. This transformation matrix is not updated during the analysis because, seismic isolators typically undergo very small rigid-body rotations.
The post-buckling behavior of the LR isolator is modeled using a very small axial stiffness () of the initial stiffness to avoid numerical convergence problems.
The mass of the LR bearing is not modeled. The user can model the mass of an isolator using inertial NodalKernels as shown in a seismic simulation example here.
References
- M. C. Constantinou, A. S. Whittaker, Y. Kalpakidis, D. M. Fenz, and G. P. Warn.
Performance of seismic isolation hardware under service and seismic loading.
Technical Report MCEER-07-0012, Multidisciplinary Center for Earthquake Engineering Research, Buffalo, New York, 2007.[BibTeX]
- I. V. Kalpakidis and M. C. Constantinou.
Effects of heating on the behavior of lead-rubber bearings i:theory.
Journal of Structural Engineering, 135(12):1450–1461, 2009a.[BibTeX]
- J. M. Kelly.
Earthquake-resistant design with rubber.
Springer-Verlag, London, 1993.[BibTeX]
- C. G. Koh and J. M. Kelly.
Effects of axial load on elastomeric isolation bearings.
Technical Report EERC/UBC-86/12, Earthquake Engineering Research Center, University of California, Berkeley, CA, 1987.[BibTeX]
- M. Kumar, A. S. Whittaker, and M. C. Constantinou.
An advanced numerical model of elastomeric seismic isolation bearings.
Earthquake Engineering and Structural Dynamics, 43(13):1995–1974, 2014.[BibTeX]
- M. Kumar, A. S. Whittaker, and M. C. Constantinou.
Seismic isolation of nuclear power plants using elastomeric bearings.
Technical Report MCEER-15-0008, Multidisciplinary Center for Earthquake Engineering Research, Buffalo, New York, 2015.[BibTeX]
- S. Nagarajaiah, A. M. Reinhorn, and M. C. Constantinou.
Nonlinear dynamic analysis of three-dimensional base isolated structures (3d-basis).
Technical Report NCEER-89-0019, National Center for Earthquake Engineering Research, Buffalo, New York, 1989.[BibTeX]
- Y. J. Park, Y. K. Wen, and A. H. S Ang.
Random vibrations of hysteretic systems under bi-directional ground motions.
Earthquake Engineering and Structural Dynamics, 14(4):543–557, 1986.[BibTeX]
- G. P. Warn and A. S. Whittaker.
A study of coupled horizontal-vertical behavior of elastomeric and lead-rubber seismic isolation bearings.
Technical Report MCEER-06-0011, Multidisciplinary Center for Earthquake Engineering Research, Buffalo, New York, 2006.[BibTeX]
- G. P. Warn, A. S. Whittaker, and M. C. Constantinou.
Vertical stiffness of elastomeric and lead-rubber seismic isolation bearings.
Journal of Structural Engineering, 133(9):1227–1236, 2007.[BibTeX]